Background
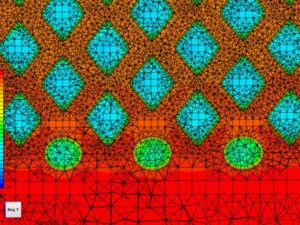
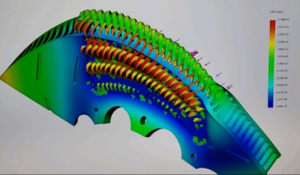
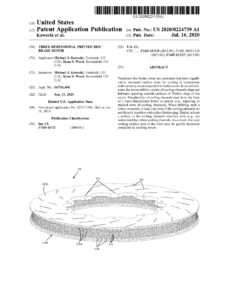
CDT is offering a high-performance sports car-oriented brake rotor. It has 2-3x less unsprung weight, faster acceleration, better handling with less dust and noise all at a competitive price. We deliver on the historical promise of aluminum brake rotors which are installed on low volume lighter production cars.
Each car’s specific brake rotors are optimally designed to dramatically improve heat dissipation via a more optimized surface area uniquely enabled by additive manufacturing or 3D printing, with stronger airflow, better thermal conductivity, and specific heat capacity. Our aluminum ceramic composite material creates a lighter design with superior high-temperature strength required by the demanding braking performance of sports car-oriented rotors. We add sophisticated heat transfer structures to the inside the vented brake rotor creating these compelling product claims.
The CRT-rotor product enables faster acceleration via less unsprung weight. For example, our rotors save ~65 pounds of rotational weight in a Dodge Challenger Hellcat. Additionally, you double the rotor life over cast iron, with 95% less dust (an environmental plus) and better car handling. The rotor design creates better heat dissipation via more heat transfer surface area, stronger airflow, 5-times better thermal conductivity along with better material diffusivity and thermal shock performance. Customers want the benefits of unsprung weight, dust reduction, handling advantages, fuel economy, service life and finally the environmental benefits of virtually no particulate emissions.
Michal J. Kawecki and Ryan S. Wood are the inventors of a patent entitled: Three-Dimensional Printed Disc Brake Rotor with a priority date of January 11, 2019. The patent cooperation treaty (PCT) was published July 16th 2020 (US 2020/0224739 A1) In December of 2020 the United States Patent and Trademark Office granted the patent (number to be assigned). Many thanks to our patent attorney and the law offices of Snell & Wilmer.
The patent claims protect key concepts around a ventilated disc brake rotor of novel design with a matrix core, that is additively manufactured with 5% to 25% aluminum ceramic metal matrix composite material. This creates a rotor with significantly increased surface areas for cooling in comparison with currently manufactured disc brake rotors. In one embodiment, the rotors utilize a matrix of cooling channels disposed between opposing outside surfaces of friction rings of the rotors. This plurality of cooling channels is in the form of a three-dimensional lattice or matrix (e.g., repeating, or stacked rows of cooling channels). When using such a lattice or matrix, at least a portion of the cooling channels do not directly interface with either friction ring; rather, they are surrounded by other cooling channels. As a result, the total cooling surface area of the rotor and material performance properties may be greatly increased compared to existing rotors.
PRODUCT PROFILE
Below is a table that maps the product features, description, advantages, and benefits for the customer. The technical specifications section has a similar comparison yet with specific scientific values contrasting cast iron and carbon fiber.
Feature | Description | Advantages | Benefits |
CDT-Rotors, Material | Proprietary ceramic aluminum metal matrix composite designed for additive manufacturing |
|
|
Exotic vented internal heat exchanger features over 1,000 radial channels | ~1-millimeter internal walls of the vented rotor with curved slots and microturbulator heat exchanger design creating patent-pending novelty. |
|
|
Customization via made to order additive manufacturing | Each rotor besides being slotted and not drilled can have unique car markings.
|
|
|
Precise tolerances and quality controls | Materials are tracked, rotors are precisely machined, serialized and processed to create traceability for every rotor |
|
|
Custom Brake Pad material | The brake pad material has been selected and optimized for our rotor material, provides a higher coefficient of friction |
|
|
Rotor Material Comparisons
Brake rotors have been made from many types of materials with different pads, stopping performance, cooling approaches, weight and reliability. There are numerous tradeoffs depending on the braking application and product design goals. The table below should clarify the details of these choices and how the customer should think about the purchase choices that are available.
Attribute | Gray Cast Iron | Carbon-Ceramic | Carbon Fiber Reinforced Ceramic | Carbon-Carbon | CDT-Rotors
Ceramic- Aluminum |
Description | Commodity cast iron for OEMs | Uses discontinuous chopped fiber pressed and resin bonded together | Interweaves continuous carbon fiber to form a 3D multi-directional matrix | Both brake pad and rotor are made from carbon fiber | Uses a proprietary metal matrix composite suitable for additive manufacturing |
Applications | Common use across industry, some performance applications | Common in sports car, aftermarket, and high-performance OEM offerings | Mostly aftermarket exotic rare and some race cars | Commonly used in Formula 1 racing | Sports car and high-performance aftermarket |
Manufacturing Time | <Hour | Weeks | Months | 5-6 Months | Hours |
Product Use Stability | Excellent-completely dense, no voids | Loses mass under hard braking, creating weight imbalances. Internal voids from incomplete resin conversion | Excellent-completely dense, no voids | Excellent-completely dense, no voids | Excellent-completely dense, no voids |
Production Technique | Cast | Mixed & pressed | Layup and pressed | Layup and pressed | Additive manufacturing |
Patented | No | No | Yes | No | Yes |
Wear life | Good | Excellent | Excellent | Poor | Excellent |
Surface Quality | Excellent | Brittle and delicate surface | Excellent | Excellent | Excellent |
Risk of chipping/dents | Low | High | Low | Low | Low |